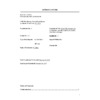 |
|
Other | Approved: 7 years ago | 613.68 kB | Comments: 0
...Development by Identification and PID Control of... ...6 4.0 Results and Discussion .......................................................................................................... 10... ...Figure 4: The Change in Temperature with... ...Figure 5: The Change in Temperature with... ...Using Proportional-Integral Controller Change to SP=60% (Kp=3;... ...Figure 6: The Change in Temperature with... ...Using Proportional-Integral-Derivative Controller Change from SP=40% to... ...to 100% step change and semi-open water... ...100% step change and semi-open water valve... ...to 65% step change and semi-open water... ...65% step change and semi-open water valve... ...to 100% step change and semi-open water... ...100% step change and semi-open water valve... ...to 100% step change and semi-open water... ...100% step change and semi-open water valve... ...to 100% step change and fully-open water... ...100% step change and fully-open water valve... ...to 100% step change and fully-open water... ...100% step change and fully-open water valve... ...Table 12: Step change from 0 to... ...Table 13: Step change from 0 to... ...Table 14: Step change from 0 to... ...Table 15: Step change from 0 to... ...the inner pipe and steam flowed in... ...between open loop and closed loop control... ...parameters of Ti and Td to evaluate... ...of P, PI and PID controllers (proportional,... ...cases were completed and analyzed. The first... ...heat 2 exchanger and the shell and... ...and the shell and tube heat exchanger... ...are possible, co-current and counter current. The... ...by the hot and cold fluid flowing... ...if the hot and cold fluids flow... ...control the temperature and pressure for the... ...open 3 loop and closed loop controllers.... ...have a feedback and the input is... ...a feedback controller and operates by identifying... ...between the output and reference input. In... ...signal is reduced and system disturbances or... ...disturbances or 5 change will not impact... ...proportional, proportional integral and 4 proportional integral... ...used in industry and from tuning operations... ...parameters such Ti and Td.The following equation... ...gain The integral and derivative gain can... ...the P, PI and PID controllers can... ...all inlet water and steam valves were... ...when turning on and off all steam... ...steam valve controller and multi-point temperature readout)... ...was turned on and the thermocouple reading... ...set to 100% and the starting water... ...the cold water and then exit through... ...steam valve 3 and then finally enter... ...valve was opened and set up to... ...set at 65% and the initial water... ...set at 100% and the starting water... ...opened three quarter and the steam controller... ...set at 3 and the Ti (Proportional... ...set at 50 and the Td (Proportional... ...set at 40% and the starting water... ...changed to 60% and with the same... ...same Kp, Ti and Td values the... ...back to 40% and Ti value was... ...with same Kp and Td values. The... ...changed to 60% and Ti value was... ...with same Kp and Td values. The... ...set at 25 and the Td value... ...the Td value change to 25. The... ...steam left over and the cold water... ...9 4.0 Results and Discussion The first... ...100% to 65%, and temperature readings were... ...65% to 100%, and the temperature readings... ...a 35% step change are seen in... ...values for step change, change in temperature,... ...for step change, change in temperature, 63.2%... ...of the step change, temperature at 63.2%... ...of the step change, time constant, and... ...change, time constant, and controller gain are... ...Steam 65% Step Change in Percent Steam... ...Final temperature 22.9 Change in Temperature 7.9... ...of the Temperature Change 4.9928 Temperature at... ...63.2% of the Change 35.8 Corresponding Time... ...the controller gain and time constant value... ...values for step change, change in temperature,... ...for step change, change in temperature, 63.2%... ...of the step change, temperature at 63.2%... ...of the step change, time constant, and... ...change, time constant, and controller gain are... ...Steam 100% Step Change in Percent Steam... ...Final temperature 32.6 Change in Temperature 9.6... ...of the Temperature Change 6.0672 Temperature at... ...63.2% of the Change 29.1 Corresponding Time... ...the controller gain and time constant value... ...of each other, and are mirror image... ...value of 30°C, and continues to decrease... ...value of 23°C, and continues to increase... ...gain are 0.23 and 0.27 for runs... ...for runs 1 and 2, respectively. The... ...constant are 0.60 and 0.55 for runs... ...for runs 1 and 2 respectively. This... ...different flow rates, and the change in... ...rates, and the change in set point... ...of 0.92 gal/s and 0.25 gal/s are... ...of 0.92 gal/s and 0.25 gal/s is... ...values for step change, change in temperature,... ...for step change, change in temperature, 63.2%... ...of the step change, temperature at 63.2%... ...of the step change, time constant, and... ...change, time constant, and controller gain for... ...Steam 100% Step Change in Percent Steam... ...Final temperature 32.6 Change in Temperature 9.6... ...of the Temperature Change 6.0672 Temperature at... ...63.2% of the Change 29.1 Corresponding Time... ...Steam 65% Step Change in Percent Steam... ...Final temperature 32.0 Change in Temperature 8.8... ...of the Temperature Change 5.5616 Temperature at... ...63.2% of the Change 28.8 Corresponding Time... ...the controller gain and time constant value... ...the controller gain and time constant value... ...the controller gain and time constant values... ...The controller gain and time constant values... ...values are 0.27 and 0.55 for the... ...at 0.92 gal/s, and 0.25 and 0.48... ...gal/s, and 0.25 and 0.48 for the... ...water flow rate and heat transfer coefficient,... ...demonstrates the temperature change of a P... ...Figure 4: The Change in Temperature with... ...demonstrates the temperature change of a PI... ...set at 3, and two Ti values... ...values of 25 and 50 are used.... ...Figure 5: The Change in Temperature with... ...Using Proportional-Integral Controller Change to SP=60% (Kp=3;... ...Figure 6: The Change in Temperature with... ...Using Proportional-Integral-Derivative Controller Change from SP=40% to... ...not oscillate over and under the desired... ...values, of 25 and 50. As per...
| N/A |
215
|
cloveb
|